Workflow
Movement of product through a facility can make or break lean goals. PROMATION Inc. demonstrated a dual-operator hand insertion solution with programmable slide shuttles for
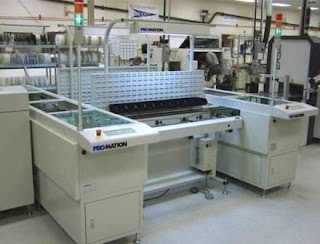
Ken Bliss, president and Shana Bliss, sales manager at Bliss Industries Inc., discussed the FLEXconveyor, a flexible box build factory on wheels has multiple patents pending on its flexible platform. The conveyor is designed to be able to bend up to 90° and features quick-clamp connectivity, the ability to support a 19" rackmount chassis, and can be configured without the use of tools or bolts. Users can start with as small as a 10 × 8 ft line and add on other sections and elements, such as the flexconveyor pickup station. The metal parts are zinc-plated with ESD-safe drag chain. Locking casters hold the completed conveyor configuration in place. “The goal is to relieve bottlenecks and eliminate waste in production lines,” says Ken Bliss, adding that it meets the modern assembler’s need to change the line on the fly and increase production rates. “We configure exactly what a customer wants, visually, on the computer system,” said

Storage
Inventory kills lean, so the saying goes. However, there are some products that must be kept in stock, such as stencils, board fixturing, wave solder pallets, etc. And when inventory does come into the factory, dealing with it efficiently can save from incoming inspection to rework/scrap.
DEK has a product to minimize the footprint of stencil storage. The Vector Guard stencil fixturing system is a model for looking at tooling less as a consumable and more as part of the factory floor. The fixed frame and interchangeable foils stencil holder uses vacuum — via a simple air pump — to tension the stencil onto the frame. It holds position and tension better than mesh-mount designs, said Brian Lau, GM of the Americas and David Byrd, U.S. operations manager at DEK. It also frees up an enormous amount of storage in the stencil holding area, as one frame is reusable and does not have to be stored with the foils. To make adoption easier, the air-tensioned VectorGuard can be cleaned like a mesh-mount stencil, can be used with the same variety of stencil foil materials, and integrates easily into printer platforms.
When dealing with incoming inventory and kitting, flexible and value-added storage products can enhance the final assembly reliability, throughput, and traceability.
Component storage involves one part to one location, said Ron Wrable, director of sales, Inovaxe. The company’s products manage WIP inventory by assigning each product a barcode and combining Web-based software as a service (SaaS) INOVISION and INOKIT with on-floor component storage, kitting, and delivery system INOCART. AN INOCART MSD also is available for moisture-sensitive components (MSDs) that will be compromised by time spent unprotected in the factory environment. Other MSD cabinet makers, such as Totech, explain that desiccant cabinets simplify inventory management logistics, since components can stay in tape-and-reel storage, and the added step and capital equipment investment of drying ovens are circumvented. Totech’s MSD storage cabinets can be configured as simple component stocking areas, MSD dryers (desiccant and low heat), or N2 environment storage. “When MSD cabinets are not in use they are not wasted space,” agreed Michelle Ogihara, sales and marketing manager, Seika, pointing out that “the McDry cabinet is designed for MSD electronics, so its recovery time is faster and its relative humidity (RH) settings are very precise. However, when MSDs aren’t in stock, it can be plain component storage, with the ergonomic design and adjustable shelves aiding manufacturers even without baking or desiccant features in use.” Understanding the range of customer needs and facility designs, McDry is manufactured in tabletop size, feeder-storage capacity, up through very large units.
“WIP is killing U.S. assemblers’ efficiency,” said Ken Bliss, while discussing the future of the American electronics manufacturing plant. Rather than changing the plant’s address — either to a larger facility or to an offshore location — first consider what can be done to make product flow better from incoming inventory to final assembly/box build.
By Meredith Courtemanche, managing editor

No comments:
Post a Comment